In recent years, I’ve been increasingly contacted by building designers perplexed by strange stripes or patterns on their glass façades. The common question: "Is this acceptable, and how can I get rid of it?"
This phenomenon is known as iridescence. Iridescence, or anisotropy, occurs due to stress differences in tempered glass, becoming visible under certain lighting and viewing conditions. It can be particularly noticeable when:
The degree of polarization is high
The glass is near the seaside
It’s 2 to 3 hours before sunset
The glass is observed from a low angle
Iridescence is more pronounced in thicker glass (8-15 mm) and heat-strengthened glass. If the tempering process isn’t optimized, it can exacerbate this effect. While iridescence doesn’t compromise the structural integrity of the glass, it does make it appear lower in quality, which is undesirable for high-end applications.
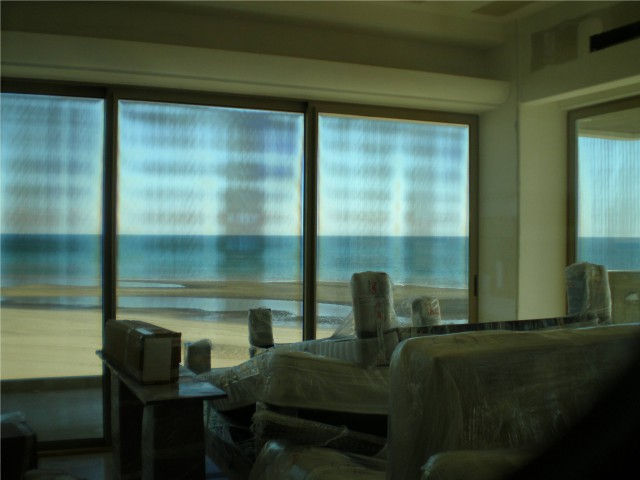
Types and Causes of Iridescence
To effectively reduce iridescence, it's essential to understand its causes. Iridescence is primarily due to uneven heating or cooling during the tempering process. This means both heating and quenching need to be uniform. If the glass is uniformly heated and cooled, iridescence should theoretically not occur. However, in practice, achieving perfect uniformity is challenging.
Heating-Related Iridescence
One significant cause of iridescence is uneven heating. For example, overly strong local convection heating can create temperature differences within the glass, leading to iridescence during quenching. If different parts of the glass are heated unevenly, these variations will manifest as iridescence.
Quenching-Related Iridescence
Non-uniform cooling during the quenching process also contributes to iridescence. This can be due to inconsistent air flow from the quench nozzles or the cooling effect of the rollers. Any non-uniformity during this phase will appear as iridescence on the glass surface.
5 Ways to Reduce Iridescence in Tempered Glass
Now, let's discuss practical steps to minimize iridescence in your tempered glass:
1. Identify the Problem Source
Determine whether the issue originates from the heating or cooling phase. Compare your glass results with reference images to pinpoint the problematic process. Once identified, focus on optimizing that specific phase.
2. Optimize Heating
Decrease Furnace Temperature: Lowering the temperature and increasing heating time helps achieve more uniform heating, improving overall glass quality.
Increase Oscillation Length: Set the longest possible oscillation length in your furnace. Use the “crawling function” if available to minimize stopping points and ensure your furnace program supports alternating stopping points.
3. Improve Quenching
Clean Quench Nozzles: Regularly clean the nozzles to ensure there are no blockages that could cause uneven air flow.
Optimize First Stopping Point: Adjust the transfer speed to quench at a low level. Aim to have the first stopping point at the lowest possible temperature to reduce stress variations.
4. Maintain Your Equipment
Regular maintenance of your tempering equipment is crucial. Running with broken heaters or faulty components can impair your ability to uniformly heat the glass, leading to increased iridescence. Ensure all parts of your equipment are in good working order.
By following these steps and maintaining your equipment, you can significantly reduce iridescence in your tempered glass, enhancing its aesthetic and structural quality.
Comments