The design and production of windshields for buses—whether for long-haul or city use—have evolved significantly over the years. Today, these essential components require more advanced technology to meet stricter environmental regulations, production standards, and the growing demand for passenger comfort and safety. By adopting modern glass technologies, glass processors can effectively cater to the distinct needs of both bus segments while remaining competitive in a rapidly changing market.

Key Trends in the Bus Market
Globally, the bus industry is increasingly focused on energy efficiency, reducing CO2 emissions, and minimizing manufacturing costs. These trends are shaping the design of bus windshields, which must balance performance with environmental considerations.
The bus market can be divided into two primary segments, each with unique requirements:
Long-Haul Buses: Primarily operated by private companies for long-distance services, these buses require advanced aerodynamics to reduce fuel consumption and noise, as well as a focus on passenger comfort and aesthetics.
City Buses: Used for local transportation in urban areas, these buses are operated by public service companies. While the focus is on cost-effective solutions, the demand for fuel efficiency and lightweight structures remains, requiring the use of thinner glass and simplified shapes for windshields.
As the global bus windshield market remains relatively niche, glass processors need to serve both segments effectively. To remain competitive, they must have equipment capable of handling small production runs and even single-piece custom orders.
From Single Windshields to Mass Production
The process of bending glass into its final windshield shape is critical. A failure during this stage compromises the optical quality, installation fit, and overall functionality of the windshield. Traditionally, bus windshields were produced using slow, low-yield, single-chamber furnaces, which were typically suited for complex or low-volume shapes. These furnaces allowed manual intervention at various stages but were not ideal for high-volume production.
In the early 2000s, serial production furnaces for bus windshields emerged. These furnaces offered several advantages:
Increased Productivity: The bending section, which is the most expensive part of the process, is only used at the final stage, making the overall process more energy-efficient.
Improved Repeatability: Serial furnaces maintain consistent heating conditions, resulting in better product yield.
Space Efficiency: These furnaces occupy less factory space and can be expanded later as needed.

Advancing Serial Production for Complex Shapes
To accommodate more complex windshield shapes, modern serial furnaces have evolved to offer better heat control, mold technologies, and improved process monitoring. For demanding shapes, such as bus windshields with tight contours or curved designs, advanced heating techniques are essential.
Focused Heat Distribution: Bending sections use highly focused heat, often with multiple upper and lower heating zones, to ensure precise shaping.
Reflective Technology: Reflective plates and parabolic grooves can optimize heat distribution and reduce energy loss, further improving efficiency.
Aggressive Heating for Tight Folds: Special heating methods and mold designs can intensify heat on the lateral folds of windshields, essential for more complex shapes.
The Role of Mold Technology
Alongside heat control, mold technology is a crucial factor in shaping bus windshields. Large, thin glass panels require careful support during the preheating phase and gradual release during the bending process. Automatic mold supports and adjustable heating controls are now standard in modern systems, allowing for greater precision and repeatability.
For complex shapes, especially windshields with tight wings, automatic wing control devices have been introduced to ensure uniform shaping. These systems can adjust mold supports during the process, ensuring that each windshield is consistently shaped to exact specifications.
Combining Control Systems for Optimal Results
Precision in both shape and optical quality is paramount in the bus windshield market. Advances in control systems now allow glass processors to achieve greater accuracy and consistency. The process is controlled based on preprogrammed recipes that define heating patterns, timing, and cooling phases. For optimal results, temperature and time-based control are combined with glass position monitoring to enhance repeatability.
A symmetrical heating system is used to ensure even heat distribution, especially when bending two glass halves in the same furnace. This system uses pyrometers to measure temperature differences between each half and adjusts accordingly to maintain balance throughout the process.
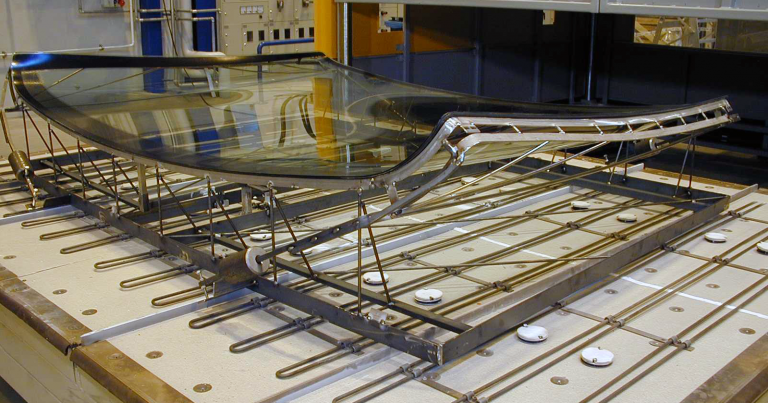
Adapting to New Bus Designs and Technologies
As bus designs become more complex, the size and volume of glass used are increasing. Modern buses, especially double-decker models, may feature multiple layers of glass at the front, including the windshield, destination sign, and upper windshield glass.
Integrating new technologies, such as heating systems, coatings, antennas, and display systems, presents new opportunities for glass processors. Rather than producing standard laminated glass, processors will be asked to deliver functional components that offer additional value, such as integrated heating or communication systems.
Staying Competitive in a Changing Market
The bus windshield market is evolving rapidly, driven by the need for more advanced designs and technologies. To remain competitive, glass processors must continually adapt their equipment and processes to meet new demands. This includes developing the ability to produce custom, high-quality, complex shapes with added functionalities. By investing in modern furnace technology and process control systems, glass processors can position themselves to thrive in a market where innovation and efficiency are paramount.
Kommentare